2.1 电火花线切割机床的特点与结构
电火花线切割加工(
Wire Cut EDM
)是特种加工中电火花加工方式的一种,是
直接利用电能或热能进行加工的工艺方法。加工基本原理是利用在导丝架固定的轨
道上连续移动电极丝(钼丝
/
铜丝)为电极,与被加工材料之间,保持适当间隙的前
提下,施加足够的脉冲电压,使得电极丝与工件之间产生火花放电,蚀除被加工材
料,同时控制机床工作台运动,与电极丝的运动形成相对运动,从而达到蚀除表面、
切割成型的目的,以加工出符合用户要求的产品。电火花线切割加工过程原理如图
2-1
所示。线切割机床的加工结构如下
[25]
:
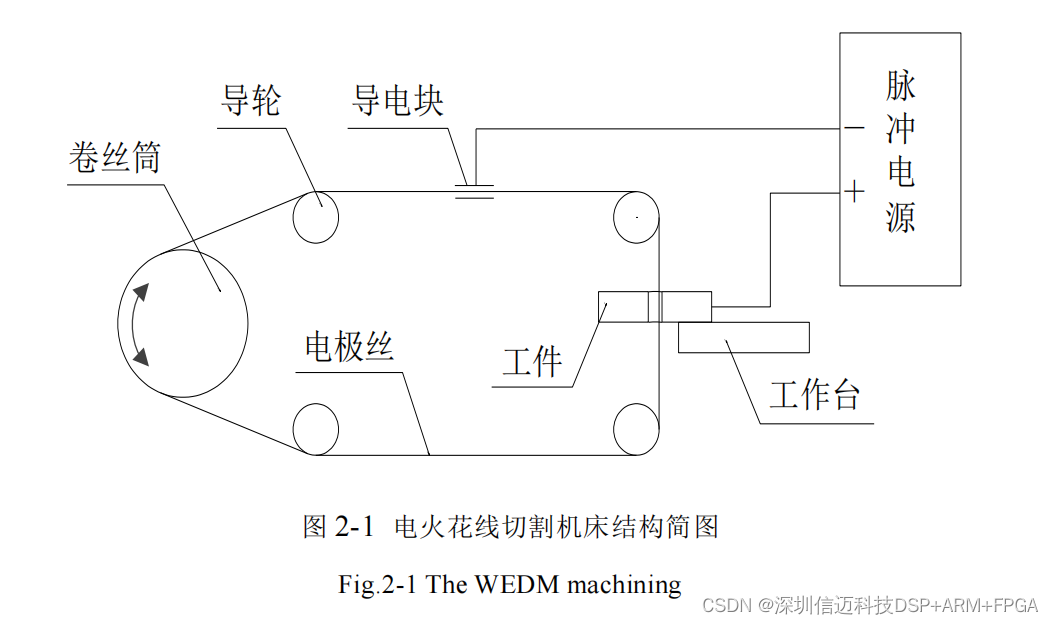
线切割机床加工方式有如下特点:
1
)不需要制作特定形状的电极,采用直径较小的电极丝不仅损耗低,且有利于
降低脉冲宽度和平均电流,工艺参数的设置范围小,从而提高了电火花加工精度,
降低成本同时缩短加工周期;
2
)线切割机床主要针对平面图形进行加工,一般复杂形腔都可加工,除了内侧
拐角有最小圆弧限制的零件,由于加工间隙与电极丝的误差存在,所以拐角圆弧必
定存在;
3
)加工过程中对工件的蚀除量少,对于贵重材料零件的试制,节约加工材料,
使得零件的试制有更多的操作空间;
4
)电火花线切割工作液采用水基液或者去离子水等,对环境无污染,对人体
无危害,过滤后可反复使用;
5
)电火花线切割机床大多具有四轴联动功能,可实现上下异形、变锥度和扭
曲曲面加工。采用移动和转动相结合方法,可加工出螺旋表面、双曲线表面等更复
杂的空间曲面。
电火花线切割机按走丝速度可分为高速往复走丝电火花线切割机(俗称“快走
丝
”
)、中走丝电火花线切割机和低速单向走丝电火花线切割机(俗称
“
慢走丝
”
)三
类。高速往复走丝电火花线切割机床是我国自主研发的机种,其结构简单、性价比
高、加工速度快,但电极丝抖动大,在加工过程中易断丝,往复使用电级丝造成的
损耗,使得产品加工质量降低。中走丝是复合走丝技术,在具有多次线切割功能的
高速走丝机中,采用
8-12mm/s
高速走丝进行粗加工,与采用
1-3mm/s
低速走丝进
行精加工,使用多次切割工艺技术,达到提高工件的表面质量及切割精度的目的。
低速单向走丝电火花线切割机床,一般以低于
0.2m/s
的切割速度作单向切割运动,
带有自动穿丝和恒张力装置,电极丝张力控制恒定无抖动、加工过程稳定、高精密
加工,采用无电阻防电解电源。
高速往复走丝电火花线切割机床由以下四部分组成
[28]
:
机床床体:床体包含机床床身、运丝筒与导丝臂组成的走丝系统和
X-Y
方向运
动工作台。床身是机床的基础,起到固定和支撑的作用,良好的床身是线切割机床
稳定运行的关键。走丝系统分为滚丝筒与导丝架,电机带动滚丝筒与导丝架上的电
极丝做往复运动,是线切割机床运动控制的一部分。
X-Y
工作台是线切割机床运动
控制的灵魂,其运动主要由两个步进电机驱动,根据数控代码驱动电机完成与电极
丝的相对运动,从而切割出所需要的工件形状和尺寸。
工作液系统:线切割工作冷却液,一般具有良好的冷却、润滑、清洗的功能,
还具备防断丝、去游离等特殊性能。工作液能帮助产品获得理想的加工光洁度,同
时提升加工效率、延长机床寿命,一般而言,普通工作液过滤后可重复多次使用。
高频脉冲电源:高频脉冲电源在加工工程中,在电极丝与被加工件之间输出高
频脉冲电压,电源正极连接被加工件或机床导电块,负极连接电极丝。可以通过脉
冲产生模块产生脉冲,通过调节脉冲信号的脉冲宽度与脉冲幅值改变电火花放电电
流大小,优秀的电源系统,可根据不同材料与不同加工需求,控制加工进给量,自
主调节输出电压。
控制系统:控制系统是线切割机床运动完成的核心,从工程图绘制到读取加工
程序代码,最后完成产品切割的加工过程中都监管控制机床的运动情况。优秀的线
切割数控专家系统,在加工过程能实时监测轨迹控制(工作台运动)与质量控制(电
源系统),检测加工中的放电间隙平均电压,能通过变频器的反馈作出响应,从而
自主调节加工进给速度
[29]
。
2.2 电火花线切割软件系统设计
本课题以高速往复走丝电火花线切割数控机床为操作对象平台,为其设计出电
火花线切割运动控制系统。电火花线切割数控系统的功能实现,需从软件层面与硬
件层面两个层面综合考虑,分别分析软硬件所需完成的功能,协同合作开发以达到
最终自动控制的目的
[30]
。系统软件层面功能实现设计如下:
软件层面功能
:
软件功能主要实现的是
CAD/CAM
功能。
CAD
功能模块实现的
功能是生成工程图,提供图形绘制功能(如矩形、圆弧、曲线等操作)与图形编辑
功能(如剪切、镜像、倒角等操作),该模块还提供了辅助功能(关键点捕捉、文
件管理等)。
CAM
模块分为参数配置、获取轨迹、代码生成、加工仿真四个部分
[25]
,
是将
CAD
模块生成的加工图形经过图元排序、轨迹偏移,加工仿真的处理后,转
换成位移增量存储到代码中,并根据生成的代码进行计算机仿真验证加工的准确性。
实现线切割机床的控制,在软件层面的要求是,必须做到能够让用户快速准确
的绘制出可用于加工的工程图,帮助用户设置相关的参数后,通过系统的加工仿真
功能,系统自动进行轨迹偏移等操作,将图元信息与位置坐标信息储存起来,供下
一步软件运动控制的调用
[32]
。软件功能实现示意图如图
2-2
所示。
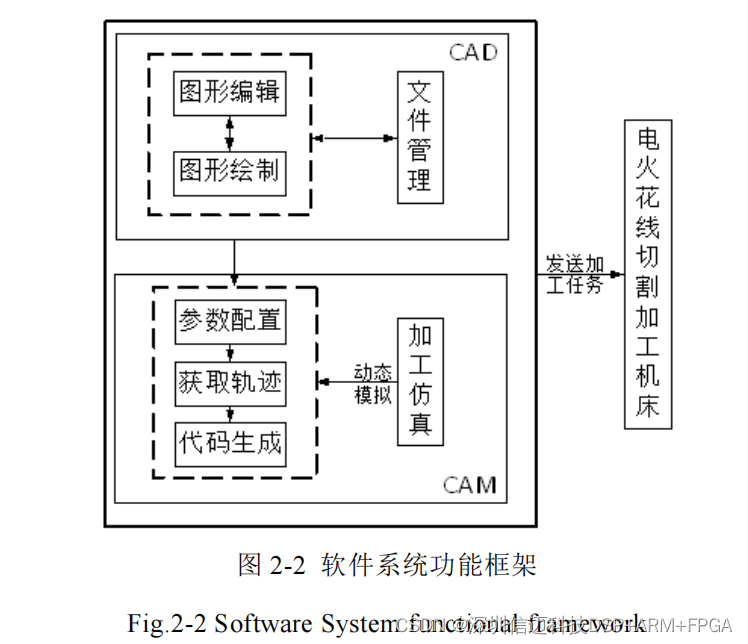
本实验室共完成了三个版本的线切割软件控制系统的开发,分别是
PC
端的开
发、
Windows CE
端的开发、
Android
端的开发与应用研究。三个版本之中,
PC
端
的软件是根源,
PC
版的
CAWEP
软件功能完备强大,之后两个版本都是基于
PC
版
开发得来,
Windows CE
端和
Android
端的软件,都实现了线切割
CAD
与
CAM
功
能,满足线切割机床软件层面的基本要求。
Android
版与
Windows CE
版的开发,实
现基本功能后,仍在优化完善,
Windows CE
端与
Android
端的软件运行如图
2-3
所
示。
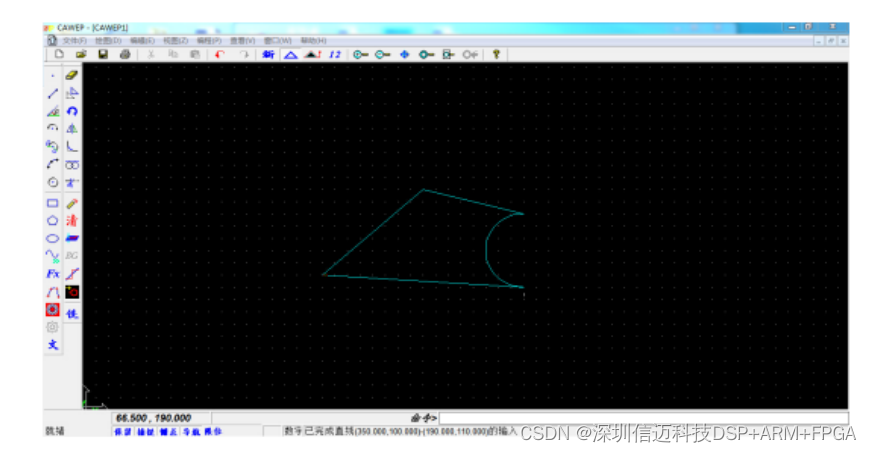
Android
平台因其开源性和丰富的硬件选择,在数控系统的开发中具备独特的
优势,
Android
系统的工控开发,很好的符合了中国制造
2025
的宗旨,也是未来工
控开发的趋势,
Android
系统在工业控制应用领域拥有巨大的发展空间
[25]
。本课题
组针对嵌入式数控系统与实际工控的需求,采用
Java
与
C/C++
混合编程方式编写
Android
版的
CAWEP
软件,为解决
Android
工控系统的稳定性与实时性难题,提供
了可行的方法,然而目前仅有少数机床厂商在研究基于
Android
的嵌入式数控系统,
市场上能支持
Android
系统的运动控制设备亦不太多
[34]
。
运行
Android
系统工业级主板也有很多尚未解决的问题,诸如底层驱动,接口
调用等,其实时性与稳定性虽得到很大的改善,但目前安卓系统的主要领域是对实
时性、实时性、功耗要求不太高,而对
GUI
有一定要求的系统上。就目前市场对工
控系统要求考虑,
Windows CE 操作系统应用于工控嵌入式设备中,仍具备很强的 竞
争力。
Windows CE
是基于
Windows PC
系统,由微软公司开发的嵌入式操作系统,其
系统定制与软件研发,都有微软公司提供的强大保障,并且
C/C++
的作为开发语言,
是机械电子控制针对底层应用最好的语言,在工控领域,仍有很大的优势。
Windows
CE
系统主要特色是结构化、模块化、多线程、抢占式多任务操作,这些特点可以
保证其应用于工业时的稳定性与实时性,并且可以直接针对底层应用开发。
Windows
CE
系统设计理念是可定制、组合和配置,
Windows CE
系统的设计理念与嵌入式初
衷一致,开发者可以根据实际的需求,开发定制最小功能系统
[35]
。
Windows CE
软件应用开发编程接近
windows
、开发周期短、系统稳定系数高,
Windows Embedded Compact 7
开始支持多核运作。工业领域要求系统平台具备实时
性、稳定性、开发环境便捷等特点,在凭借
MSMQ
(
Microsoft Message Queuing
)
先进的应用服务下,
Windows CE
系统实现了工业生产功能的全面集成,对于实时
性要求高的某些智能工控工业,
Windows CE
系统也可游刃有余。
综合考量两个嵌入式版本软件优缺点、实际开发过程的难易度、电火花线切割
机床的加工要求与市场配套应用等因素后,最终决定使用
Windows CE
版本软件
CAWEP
(
Computer Aided Wire-EDM CNC Programming System
一计算机辅助线切割
数控编程系统)软件为基础,完成后续开发,实现其运动控制的功能。
Windows CE
操作系统可以根据线切割机床的基本功能要求进行定制,保证其性能的同时,减小
功耗、启动时间等。应用软件开发过程中,可以使用的
Windows API
降低开发难度,
且市场上有大量成熟的支持
Windows CE
系统的运动控制硬件产品。
本文对
CAWEP
软件开发,使用的开发工具是
Visual Studio 2005
组件,开发过
程中常用的编辑器、调试器和编译器等组件包括都包含在
Visual Studio 2005
中,
Visual Studio 2005
包含了
VB
、
VC++
、
C#
等编译环境,对具体功能实现的代码编写
都是在
MFC
对话框的框架下完成。
MFC(Microsoft Foundation Classes)
是面向对象程序设计与
Application
framework
的完美结合,是微软公司的一个
C++
类库,它是
VC++
的核心,封装了很
多的
windows API
函数,是
C++
与
Windows API
的结合;很彻底的用
C++
封装了
Windows SDK
中的结构和功能;
MFC
多用于开发各种包含窗口、图形等可视化程
序。在
VC++
里新建一个
MFC
的工程,就等于是建立一个通用框架,此框架为开发
者完成了各种窗口、工具栏、菜单的生成和管理的初始化工作,不需要开发者再去
解决如窗口使用
Windows API
注册、生成与管理这些比较复杂但乏味基础的问题
[36]
。
MFC
生成程序框架如图
2-4
所示.
2.3 电火花线切割硬件系统设计
设计完了软件主控系统后,结合现有硬件设备,针对实际的运动控制,完成机
床各部分的运动动作,实现机床的运动控制。本文使用实验机床的福斯特
DK77
系
列快走丝机床,要想实现电火花线切割机床的运动控制,必须了解机床的基本信息、
组成结构与控制原理,机床基本信息如图
2-5
所示。
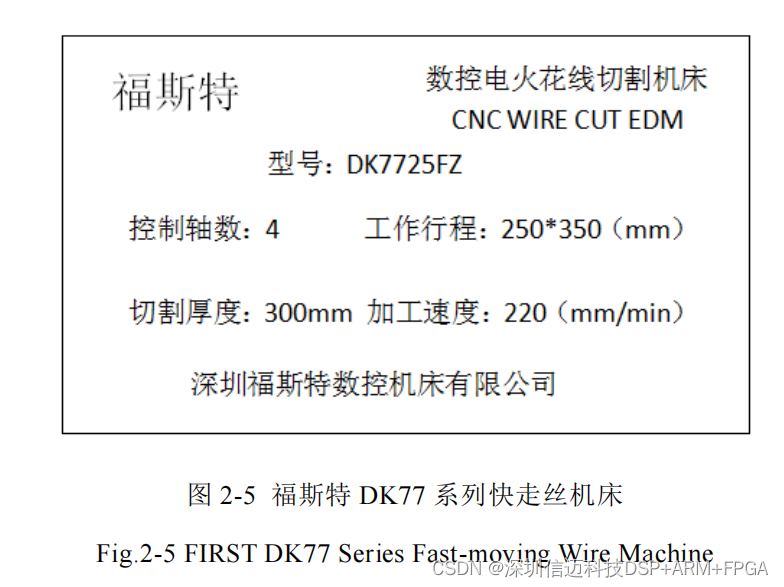
本文将硬件功能模块的设计分为以下几大模块:
1
)工作台主控系统:由
X-Y
两个方向的步进电机组成,其与电极丝的相对运动轨迹,就是产品的外形轮廓,十
字工作台的控制称为轨迹控制
[37]
;
2
)运丝系统与工作液系统:丝筒的运动带动电
极丝的运动,丝架导轨是电机丝运动路径,两者配合,决定电极丝的运动,电极丝
的张紧,震动等都会给加工质量带来影响;
3
)工作液系统:在加工过程中,向电
极丝喷射工作液,其作用是聚集电能、保护电极丝等;
4
)电源系统,电源系统负
责给电极丝提供高频脉冲电压,产生火花放电,加工过程中电压、电流、进给速度
都决定加工件的质量,所以又称电源系统为质量控制
[38]
。了解各个硬件部分的功能
需求,并为其找到出相应的控制方法,是硬件层面需要实现的功能。
线切割机床的控制,可分运动控制、电气控制和电源控制。机床工作台
X-Y
方
向的运动控制,是机床运动控制的核心,其运动主要由两个步进电机驱动,根据上
位机的数据信息完成与电极丝的相对运动,从而切割出所需要的工件形状和尺寸;
优秀的电源系统,可根据不同材料与不同加工需求,控制加工进给量,自主调节输
出电压,本课题使用电源为课题组自制电源,可以通过调节脉冲信号的脉冲宽度与
脉冲幅值改变电火花放电电流大小;机床电气控制的主要任务是控制运丝筒三相电
机的启停、调速、正反转和工作液水泵的开关。
课题执行之初,对于硬件功能实现的设计,本实验共有两套方案。其一是双核
控制单板卡,在
ARM
芯片中运行软件,得到加工数据,在
DSP
芯片中将数据转化
成加工指令,将两块芯片焊接到一块
PCB
板上,两块芯片用
SPI
总线进行通讯,要
完成以上构想,需要良好的软硬件能力。软件需要完成现有
CAWEP
软件的开发与
优化,还有底层驱动等大量程序,硬件需要打板、电路设计、元器件使用等综合能
力,目前此构想,实验室在同步进行中。
考虑到开发难度、时间与对后续开发的帮助,笔者课题最终定为,实现线切割
机床的基本功能,完成
CAWEP
软件的后续开发,使其能够实现真正的
CAM
功能,
实现机床的各个模块的控制,使得机床能正常运行,为后续的开发,奠定良好的软
硬件基础。为完成对该机床的控制,我们从以下方面完成硬件设计:
1
)工作台的运动是系统设计的核心,工作台的运动由软件系统与运动控制器共
同完成,工作台的运动的轨迹是软件系统生成的加工轨迹,我们使用支持
Windows
CE
系统的运动控制器,对该运动控制器进行二次开发,调用
API
函数,使得运动
控制器输出方向与脉冲信号,达到驱动电机运动的目的,软硬结合的开发方式,能
够使得主控系统的控制更贴合实际的工况;
2
)走丝系统、润滑系统与电源系统的相关控制,都交由变频器控制监管,只需
完成接线端子的连接,变频器可以通过外围接口电路实现控制丝筒电机变速、水泵
启停和电源保护等功能,且变频器接受上位机的命令,仅需通过接线端子接受高低
电频即可。
3
)电源则是采用由实验室自行研发的高频脉冲电源,使用
stm32
芯片作为电源
的主控控制芯片,可以调节电压、电流与脉冲等电参数,对于电源系统的监管控制,
本文中也是通过变频器完成相关部分的工作。机床硬件控制原理如图
2-6
所示。
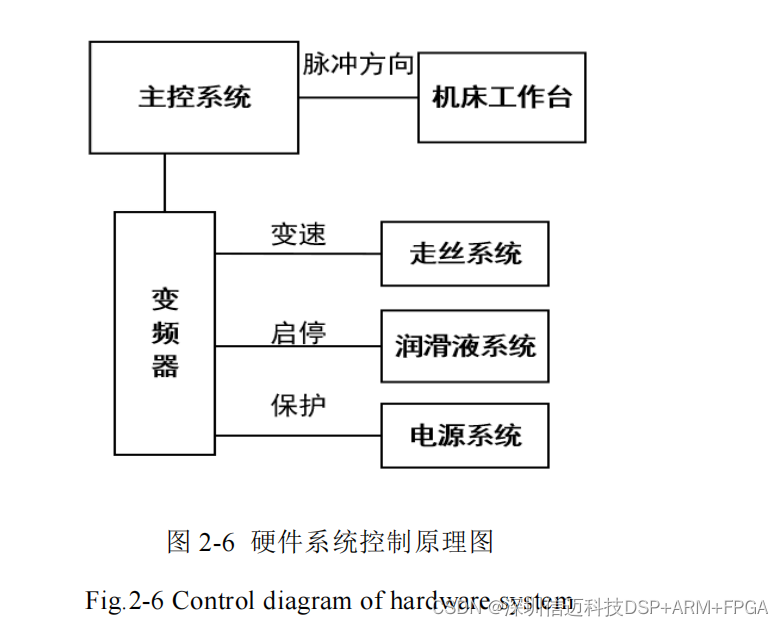
完成上述的设计之后,本文选择一款支持
Windows CE
系统的运动控制器,来
完成对工作台运动的控制,本运动控制器的设计是嵌入式工控(
ARM
架构)与运
动控制相结合,软硬件一体化方案。软件操作系统使用的是定制与配置后实现最小
功能的
WINCE6.0
操作系统,硬件部分采用
ARM
架构工控机与专用运动芯片方式
组成,既保证系统运行的稳定,又有强大的计算能力与输出能力。
本运动运动控制器,提供
4
轴联动控制;输出的脉冲的频率与电压都完全满足
不同步进驱动器的需要;支持
S
曲线加减速和
T
型加减速插补控制,可以让开发者
在开发过程中自行设计控制类型;支持任意
2
~
4
轴的直线插补与圆弧插补;提供
DLL
库与部分源码,调用相关的函数,可完成相关的运动。
运动控制器提供的运动控制函数,包括以下几个类型:脉冲输出模式的控制;
速度曲线设置,包括
S
型曲线与
T 型曲线;位移控制;检测指定轴的运动状态;轴
的运行停止;单轴运行中改变当前运行速度;改变目标位置;单轴连续运动;指定
轴加减速与停止,包括急停、缓停等不同,运动情形;设置原点信号与限位信号的
有效电平;插补运动设置,有直线,圆弧插补以及插补轴数的选择;间隙补偿值设
置。合理调用函数,可以完美的契合线切割工作台的运动控制要求。运动控制器主
板如图 2-7 所示。
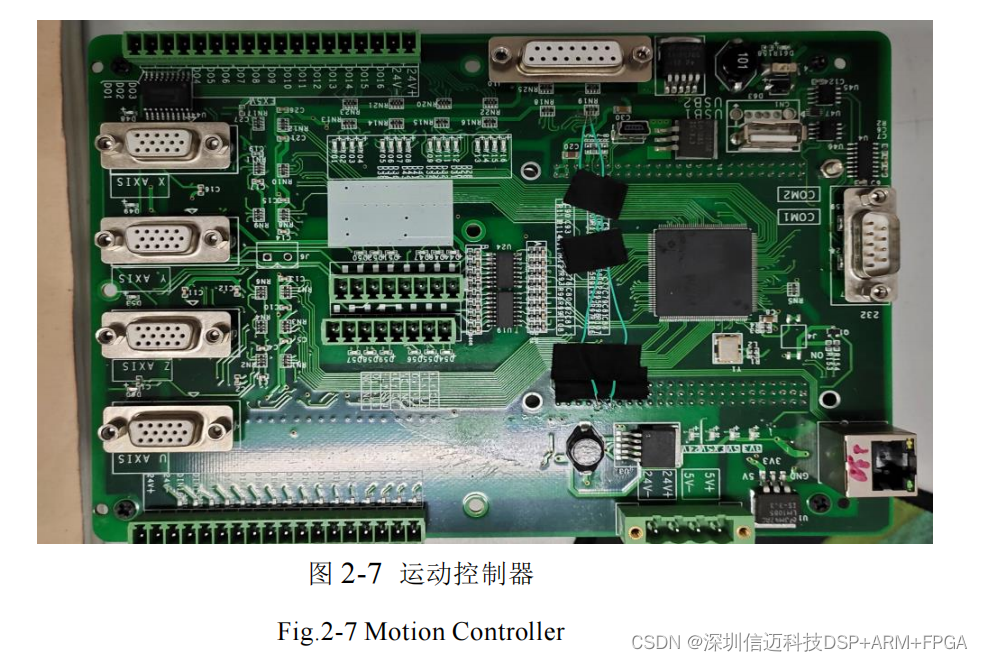
本文机床运丝系统三相电机、工作液系统水泵启停、电源保护与放电控制,都
交由变频器完成,本课题选择
SY-AX2
欣双源线切割专用变频器,如图
2-8
所示。
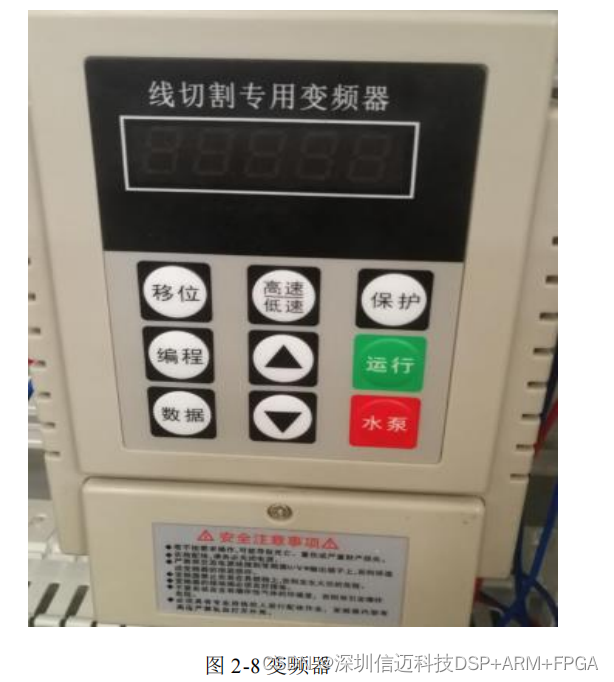
本变频器功能完备、操作简便、接口丰富,其功能介绍如下:
1
、变频器设有极性可调的左右行程、加工起停、开关高频电源等输入输出信
号开关。使用者可自行选择常开、常闭状态,以适应不同厂商的机床要求及上位机
控制信号的设计;
2
、自带完整的内部供电系统,在断丝检测电路中,无需外部供电,直接将引
脚接到对应位置上,就能完成安全、可靠的断丝检测;
3
、在调试状态下,自带信号屏蔽功能,能控制电机切换到低速状态,轻松地
完成上丝;
4
、可大范围调整电机加速度在,使得换向更快,机床效率更高,使用
3
根信
号线进行
8
段速控制,使机床能满足不同的速度需求,满足工件的加工要求,从
而提高机床的加工质量;
5
、功能控制、变频调整一体化设计。本变频器只需将相关信号直接接入对应
接口,即可实现所有控制,与通用变频器相比,省去大量的参数设置,安装使用简
单方便。
2.4 本章小结
本章中介绍了电火花线切割加工原理和特点,根据电火花线切割机床的组成和
系统功能需求分析,提出了电火花线切割机床控制的总体设计方案。在软件设计上
采用
Windows CE6.0
系统,对现有的
CAWEP
软件进行进一步的开发,软硬结合的
开发模式,使得软件开发与硬件使用更好的结合;在硬件选型上,使用采用
ARM
微处理器作为主控制板,选择支持
Windows CE6.0
系统的运动控制器,并对控制器
进行二次开发,控制工作台运动,选用线切割专用变频器作为辅助控制装置,将电
源系统、工作液系统和走丝系统的控制,都交予变频器。