本章目的:出规范的3d装配图。
4.产品装配建模:
4.1 装配体建模流程:
4.1.1 自底向上设计 bottom-up design流程:
4.1.2 自顶向下设计 top-down design建模流程:
注:这是国标《GB/T 26099-2010 机械产品三维建模通用规则》中的流程,具有一定的权威性,新手请严格按照流程来建模,老手可以查漏补缺。
4.1.3 自底向上设计 bottom-up design
独立于装配体设计各个零件,然后把设计完成的零部件自下而上地逐级装配成部件、组件直至完整的产品,其间每个零部件应符合上一层装配件规定的外形尺寸、外部接口尺寸和相对位置尺寸。
4.1.4 自顶向下设计 top-down design
设计时从系统角度入手,针对设计目的,综合考虑形成产品的各种因素(专业技术现状、工艺条件和设计手段等),确定产品的性能、组成、相互关系和实现方式,形成设计的总体方案;然后在此基础上分解设计目标给分系统具体实施,分系统从上级系统获得必须的相关参数等,并在上级系统确定的边界内开展设计,最终完成总体性能相对最优的设计。
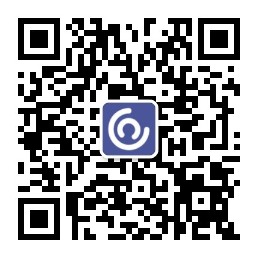
4.2 装配建模的详细要求
4.2.1 装配建模设计流程
产品的装配建模一般采用两种模式:自顶向下设计模式和自底向上设计模式。根据不同的设计类型及其设计对象的技术特点,可分别选取适当的装配建模设计模式,也可将两种模式相结合。
自底向上设计模式一般需要把所有底层零部件设计完成后才进行装配设计,其顺序是从底层向上逐级搭建产品模型。
自顶向下设计模式既能管理大型组件,又能有效地掌握设计意图。它不仅能在同一设计小组间迅速传递设计信息、达到信息共享的目的,也能在不同的设计小组间同样传递相同的设计信息,达到协同作战的目的。在开发过程中,通过严谨的沟通管理能让不同的设计部门同步进行产品的设计和开发。
4.2.2 装配建模流程的选用
两种设计模式各有特点,应根据不同的研发性质和产品特点选用合适的流程。
对于产品结构较简单或对成熟度较高产品的改进设计,可采用自底向上设计模式。对于新产品研发或包含曲面分割的产品适宜采用自顶向下的设计模式。两种设计模式并不互相排斥,在工程设计中,也常有将自顶向下设计和自底向上两种设计模式混合使用的情况。
4.2.2.1 环境参数设置。
设置方法同零件建模过程。
4.2.2.2 装配建模过程。
一般在实际的建模中是综合运用。作者在设计思路上是自顶向下设计,但产品建模时会先建立几个大的骨架零件进行装配,然后做细节追加调整。
4.2.2.3 装配体检查。


4.2.2.4 工程图出图。
4.3 装配通用原则
在装配建模设计中,应遵循以下通用原则:a)所有的装配单元应具有唯一性和稳定性,不允许冗余元素存在;
b)应合理划分零部件的装配层级,每一个装配层级对应着装配现场的一道装配环节,因此,应根据装配工艺来确定装配层级;
c)每个装配模型应包含完整的装配结构树,该结构树应包含装配信息;
d)装配有形变的装配单元(例如弹簧、锁片、铆钉和开口销等)应按安装后的变形状态进行装配;
e)装配建模过程应充分体现DFM和DFA的设计标准,应充分考虑制造因素,尽量提高其工艺性能;
4.4 装配总体要求
在装配建模设计中,应遵循以下总体要求:a)装配建模应采用统一的量纲,长度单位通常设为毫米,质量单位通常设为千克;
b)模型装配前,应将装配单元内部的与装配无关的基准面、轴、点及不必要的修饰进行消隐处理,只保留装配单元在总装配时需要的基准参考;
c)为了提高建模效率和准确性,零件级加工特征允许在装配环境下采用装配特征建构,但所建特征必须反映在零件级;
d)装配工序中的加工特征在零件级应被屏蔽掉;
e)在自顶向下设计时,可在布局设计中,将关键尺寸定义为变量,以驱动整个产品的设计、修改;
f)只有在装配模型中才能确定的模型尺寸,可采用关系式或参照引用的方式进行设定,必要时可加注释;
g)复杂结构装配时,可采用简化表示法,提高系统加载和编辑速度;
h)在进行模型装配前,应建立统一的颜色和材质要求,给定各种漆色对应的RGB色值和材料纹理,以保证各型号的产品外观的一致性;
i)装配模型应包含三维爆炸图状态,以便快速示意产品结构分解和构成;
j)每一级装配模型都应进行静、动态干涉检查分析,必要时,应按GB/T 26101中的规定进行装配工艺性分析和虚拟维修性分析。
4.5 装配层级定义原则
每一个装配模型对应着产品总装过程中的一个装配环节。根据实际情况,每个装配环节又可分解为多个工序。在分解工序和工步过程中应遵循DFA原则:a)根据生产规模的大小合理划分装配工序,对于小批量生产,为了简化生产的计划管理工作,可将多工序适当集中;
b)根据现有设备情况、人员情况进行装配工序的编排。对于大批量生产,即可工序集中,亦可将工序分散形成流水线装配;
c)根据产品装配特点,确定装配工序,例如,对于重型机械装备的大型零组件装配,为了减少工件装卸和运输的劳动量,工序应适当集中,对于刚性差且精度高的精密零件装配,工序宜适当分散。
4.6 装配约束的总体要求
装配约束的选用应正确、完整,不相互冲突,保证装配单元准确的空间位置和正确的运动副定义。装配约束的定义应符合以下要求:4.7 装配模型中的机构运动分析基本要求
装配模型中的机构运动分析应符合以下要求:
a) 针对具有运动机构的区域,定义装配约束关系、运动副类型、机构的极限位置;
b) 对运动机构进行运动过程模拟,进行碰撞检查和机构设计合理性分析,并将分析结果反馈到设计,并做出设计决策;
c) 对产品各装配区域进行机构运动分析,直到干涉、碰撞等问题完全解决。
4.8 装配结构树的管理要求
装配结构树的管理应符合以下要求:
a) 装配结构树应能表达完整有效的装配层次和装配信息;
b) 应对零、部件模型在装配结构树上相应表达的信息进行审查;
c) 完成模型装配后,应对模型的装配结构树上的所有信息进行最终的检查。
4.9 模型封装
模型的封装应符合下列要求:
a) 简化的实体在移去内部细节的同时应提供正确封装;
//给客户时尤其需要,不能将产品内部信息暴露。
b) 对模型进行容积和质量特性分析时,可以封装模型;
c) 为消隐专利数据,实体可以在提供给供应商或子合同商之前简化或去除专利细节;
d) 用于有限元分析的模型可以进行封装。